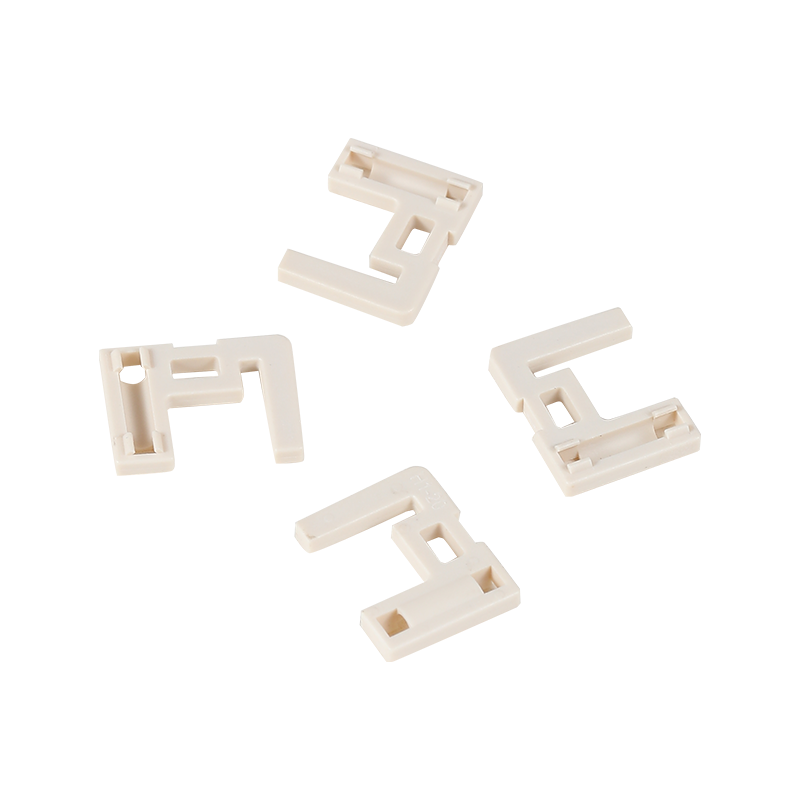
The automotive industry is a cornerstone of modern manufacturing, with a complex supply chain that relies heavily on precision engineering and advanced materials. At the heart of this industry lies the production of auto parts moulds, which are essential for creating the components that make up a vehicle. Among these, car bumper moulds and injection moulding automotive parts stand out for their critical role in both the safety and aesthetics of vehicles.
Auto parts moulds are the backbone of the automotive manufacturing process. They are used to produce a wide array of components, from small fasteners to large body panels. The precision and detail of these moulds directly impact the quality and performance of the final product. Moulds are designed to withstand high pressures and temperatures, ensuring that the parts produced are consistent and reliable.
Car bumper moulds are a specific type of auto parts mould that is crucial for both the safety and aesthetic appeal of vehicles. Bumpers are designed to absorb impact during collisions, protecting the vehicle's body and its occupants. The moulds used to create these components must be robust and capable of producing parts with high durability and structural integrity. Modern car bumper moulds also incorporate elements of aerodynamics and style, reflecting the vehicle's design language.
Injection moulding is a manufacturing process that involves injecting molten material into a mould, where it cools and hardens to take the shape of the mould's cavity. In the automotive industry, this process is used to produce a vast array of parts, from interior components to exterior trim. The advantages of injection moulding include high production efficiency, the ability to create complex shapes, and the use of a variety of materials, including plastics and metals.
The choice of material for injection moulding automotive parts is critical. Materials must be chosen based on their strength, durability, and resistance to environmental factors such as temperature and moisture. Plastics are commonly used due to their lightweight nature and ease of moulding, while metals are chosen for their strength and heat resistance, particularly for components that require high durability.
The advantages of using injection moulding in the automotive industry are manifold. It allows for the mass production of complex parts with a high degree of precision. The process also enables the creation of parts with intricate details and designs, which can enhance the vehicle's appearance and functionality. Additionally, injection moulding can reduce waste and material costs, as the process is highly efficient and produces small scrap.
Despite the many benefits, injection moulding in the automotive industry also faces challenges. One of the main issues is the high initial cost of moulds, which can be a barrier for smaller manufacturers. However, the long-term cost savings and efficiency gains often offset this initial investment. Another challenge is the need for precise temperature and pressure control during the moulding process, which requires sophisticated machinery and skilled operators.
Advancements in materials science are pilot the development of new, lightweight materials that can improve fuel efficiency and performance. Additionally, the rise of electric vehicles is driving the need for moulds that can produce components specific to these vehicles, such as battery casings and electric motor housings.
In conclusion, auto parts moulds, including car bumper moulds, are integral to the automotive industry. They enable the production of high-quality, reliable components that are essential for the safety, performance, and aesthetics of vehicles. Injection moulding, with its efficiency and versatility, is a key process in this manufacturing landscape.