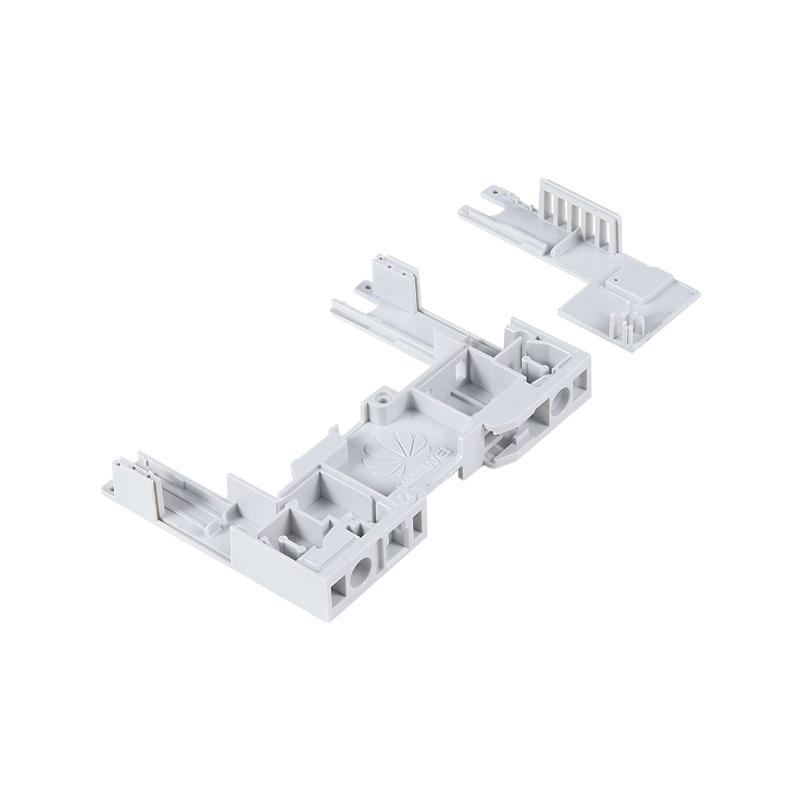
Plastic molding is a widely used manufacturing process that produces a variety of components for industries such as electronics, automotive, medical, and consumer goods. Among the different types of molds, case plastic molds are particularly important for creating protective enclosures, housings, and structural parts. These molds ensure precision, durability, and efficiency in mass production.
Case plastic molds represent the cornerstone of modern protective enclosure manufacturing, utilizing advanced injection molding techniques to produce durable, high-precision components. These custom-engineered tools transform molten polymers into complex geometries with exceptional dimensional accuracy, making them indispensable for electronics, medical devices, and industrial equipment.
Case plastic molds are specialized tools used in injection molding to produce protective enclosures, housings, and structural components for various industries. These molds are designed to shape molten plastic into precise forms, ensuring durability and consistency in mass production.
Made from hardened steel or aluminum, case plastic molds withstand high pressure and repeated use while maintaining accuracy. The injection molding process involves heating plastic pellets, injecting the melted material into the mold cavity, and cooling it to form the final product.
Key benefits of case plastic molds include high precision, cost-efficiency for large-scale production, and design flexibility for complex geometries. They are widely used in electronics (e.g., device covers), automotive (e.g., dashboard parts), medical (e.g., equipment housings), and consumer goods (e.g., storage containers).
With advancements in mold design and materials, case plastic molds continue to enhance manufacturing efficiency and product quality across multiple sectors.
A case plastic mold is a specialized tool designed to shape molten plastic into a specific form, typically used for protective casings. The process involves injecting heated plastic material into a mold cavity, where it cools and solidifies into the desired shape. The mold itself is usually made from hardened steel or aluminum to withstand high pressure and repeated use.
Key Advantages of Case Plastic Molds:
High Precision and Consistency:
Modern molding techniques allow for tight tolerances, ensuring that each produced part meets exact specifications.
Automated systems reduce human error, leading to uniform product quality.
Once the mold is created, the per-unit cost decreases significantly with higher production volumes.
Reduced material waste compared to other manufacturing methods.
Design Flexibility:
Complex geometries, undercuts, and fine details can be incorporated into the mold design.
Custom textures, logos, and surface finishes can be directly molded into the product.
Durability and Longevity:
High-quality molds can last for hundreds of thousands of cycles with proper maintenance.
Resistant to wear and corrosion, ensuring stable performance over time.
Case plastic molds are used in various industries, including:
Electronics: Smartphone cases, battery covers, and connector housings.
Automotive: Dashboard components, sensor enclosures, and interior trim parts.
Medical: Device housings, surgical instrument casings, and disposable equipment.
Consumer Goods: Appliance covers, tool cases, and storage containers.
Several factors contribute to the effectiveness of a case plastic mold:
Material Selection: The choice of plastic (e.g., ABS, polycarbonate, or nylon) affects strength, flexibility, and heat resistance.
Mold Design: Proper gate placement, cooling channels, and ejection mechanisms impact production efficiency.
Maintenance: Regular cleaning and inspection prevent defects and extend mold life.
Case plastic molds play a crucial role in modern manufacturing by enabling the efficient production of high-quality plastic components. Their ability to deliver precision, cost savings, and design versatility makes them indispensable across multiple industries.