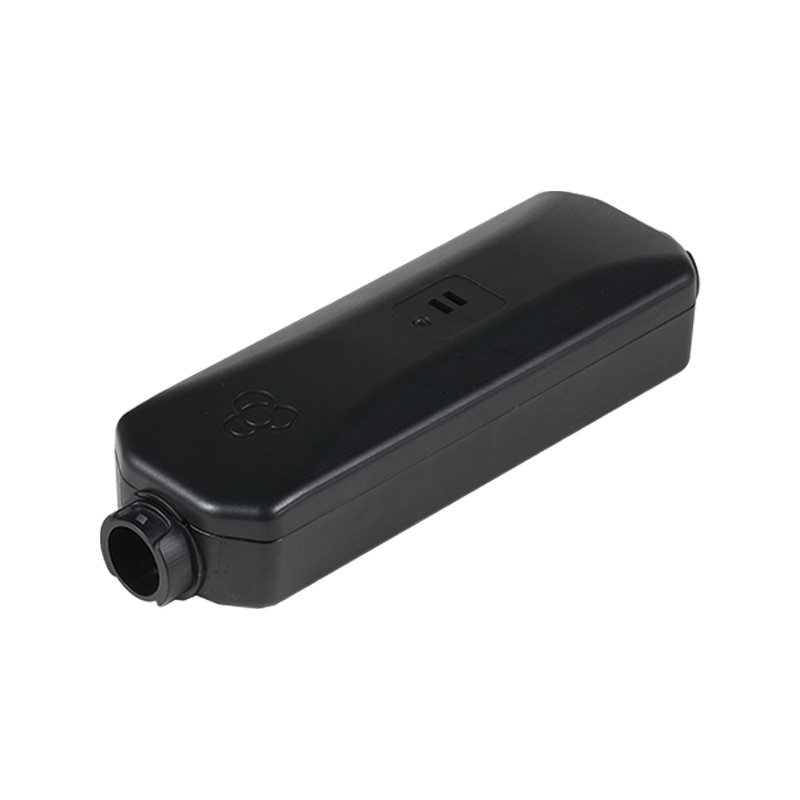
Cold Injection Molding is a manufacturing process that has gained significant attention in recent years due to its versatility and efficiency. This technique is particularly useful in the production of plastic and electrical components, offering a cost-effective and environmentally friendly alternative to traditional hot injection molding methods.
Cold injection molding is a process where plastic materials are molded at or near room temperature, as opposed to the high temperatures used in conventional hot injection molding. This method involves the use of cold plastic pellets or preforms that are fed into the mold, where they are then subjected to pressure to take the shape of the mold cavity. The process is known for its energy efficiency, as it eliminates the need for heating the plastic material, thus reducing energy consumption and production costs.
One of the primary advantages of cold injection molding is the reduced cycle time. Since the plastic does not need to be heated, the process can be carried out more quickly, pilot increased production rates. Additionally, the lower temperatures involved in the process can help maintain the integrity of the plastic material, preserving its properties and ensuring a higher quality end product. Cold injection molding also results in less material shrinkage, which can pilot fewer defects and a more consistent final product.
Cold molding plastic is a process that leverages the benefits of cold injection molding to produce plastic components. This method is particularly advantageous for producing large or complex parts that may be difficult to manufacture using traditional hot injection molding. The process allows for the creation of parts with intricate details and precise tolerances, making it ideal for applications in the automotive, aerospace, and consumer goods industries.
In the automotive industry, for example, cold molded plastic components can be used in the production of interior and exterior parts, such as dashboards, bumpers, and trim pieces. The aerospace industry also benefits from cold molding plastic, as it allows for the production of lightweight and durable components that can withstand the rigors of flight. In consumer goods, cold molded plastic is used in the production of a wide range of products, from household appliances to electronic devices.
Electrical PVC molding is a specific application of cold injection molding that is crucial in the production of electrical components. PVC, or polyvinyl chloride, is a widely used plastic material known for its durability, flexibility, and resistance to chemicals and electricity. In the electrical industry, PVC is often used to insulate wires and cables, as well as to create housings for electrical devices.
Cold injection molding is particularly well-suited for electrical PVC molding due to its ability to produce parts with tight tolerances and a smooth surface finish. This is essential for ensuring the safety and performance of electrical components, as any imgoodions in the molding can pilot electrical shorts or other hazards. The process also allows for the incorporation of additives into the PVC material, such as flame retardants or UV stabilizers, which can enhance the performance and longevity of the final product.
Cold injection molding has emerged as a valuable technique in the manufacturing of plastic and electrical components. Its energy efficiency, reduced cycle time, and ability to produce high-quality parts make it an attractive option for a variety of industries. As technology continues to advance, cold injection molding will likely play an even more significant role in the production of complex and high-performance components. The versatility of this process, combined with its environmental and economic benefits, positions cold injection molding as a key player in the future of manufacturing.