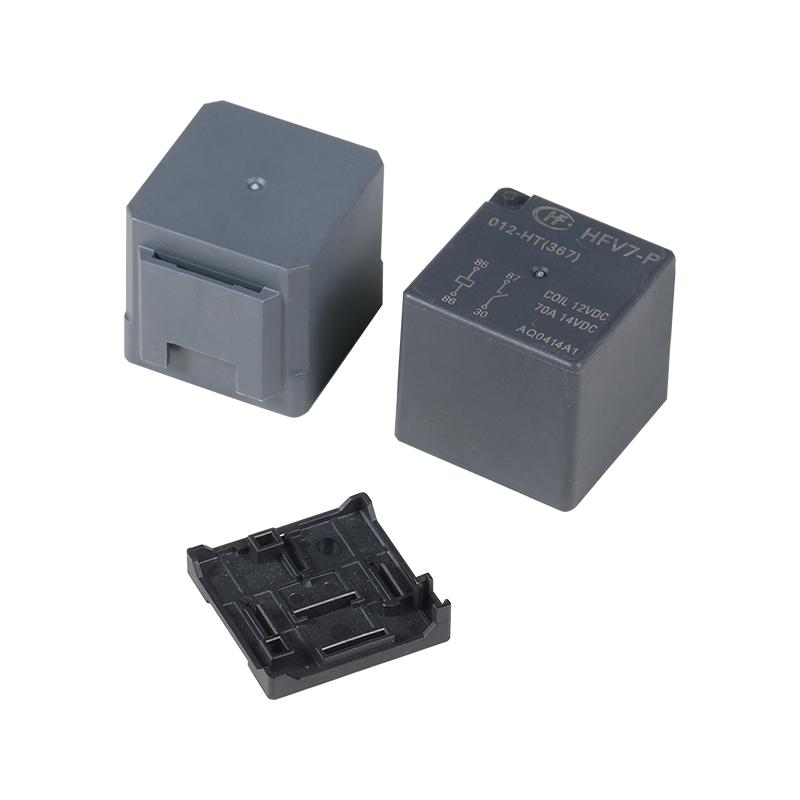
The automotive industry is a cornerstone of modern manufacturing, and the production of automotive parts is a complex process that requires precision, efficiency, and innovation. Injection molding is a key technology in this field, offering a range of benefits that have made it an indispensable method for producing a variety of car parts.
Injection molding is a manufacturing process that involves injecting molten material, typically plastic or thermoplastic polymers, into a mold to create a variety of shapes and parts. In the automotive industry, this process is used to produce a wide array of components, from small interior fittings to large exterior panels. The versatility of injection molding allows for the creation of complex geometries with high precision, making it an ideal choice for the intricate parts found in vehicles.
One of the primary advantages of injection molding in automotive parts production is the ability to create parts with high dimensional accuracy and repeatability. This ensures that each part produced is consistent, which is crucial for assembly and performance. Additionally, the process allows for the use of a variety of materials, enabling manufacturers to select the more suitable material for each specific part based on factors such as strength, weight, and resistance to environmental conditions.
The efficiency of the injection molding process also contributes to cost savings. Since the process is highly automated, it reduces labor costs and can produce parts at a faster rate than traditional manufacturing methods. This speed of production is particularly important in the automotive industry, where meeting demand and maintaining a steady supply chain are critical.
Injection molding is used to produce a vast array of car parts, from simple components like buttons and knobs to more complex parts such as dashboards and bumpers. The process is particularly well-suited for producing parts with high detail and intricate designs, which are common in modern vehicles. For example, the textured surfaces and detailed logos found on car interiors are often created through injection molding.
The use of injection molding in car part production also offers environmental benefits. The process can utilize recycled plastics, contributing to a more sustainable manufacturing process. Furthermore, the lightweight nature of many plastics used in injection molding can help reduce the overall weight of vehicles, pilot improved fuel efficiency and reduced emissions.
Creating a mold for automotive parts is a meticulous process that requires careful design and engineering. The mold must be designed to withstand the high pressures and temperatures involved in the injection molding process while also ensuring that the part produced is free from defects. This often involves the use of computer-aided design (CAD) software to create a detailed model of the part, which is then used to create the mold.
Once the design is finalized, the mold is typically made from steel or aluminum, depending on the specific requirements of the part and the production volume. The mold is then machined to the exact specifications of the part, ensuring that it can produce the desired shape and detail. After the mold is created, it is tested and refined to ensure that it can produce parts with the required quality and consistency.
Injection molding is a critical technology in the automotive industry, offering a range of benefits that make it an essential method for producing car parts. Its versatility, efficiency, and ability to produce high-quality parts have solidified its place in the manufacturing process.