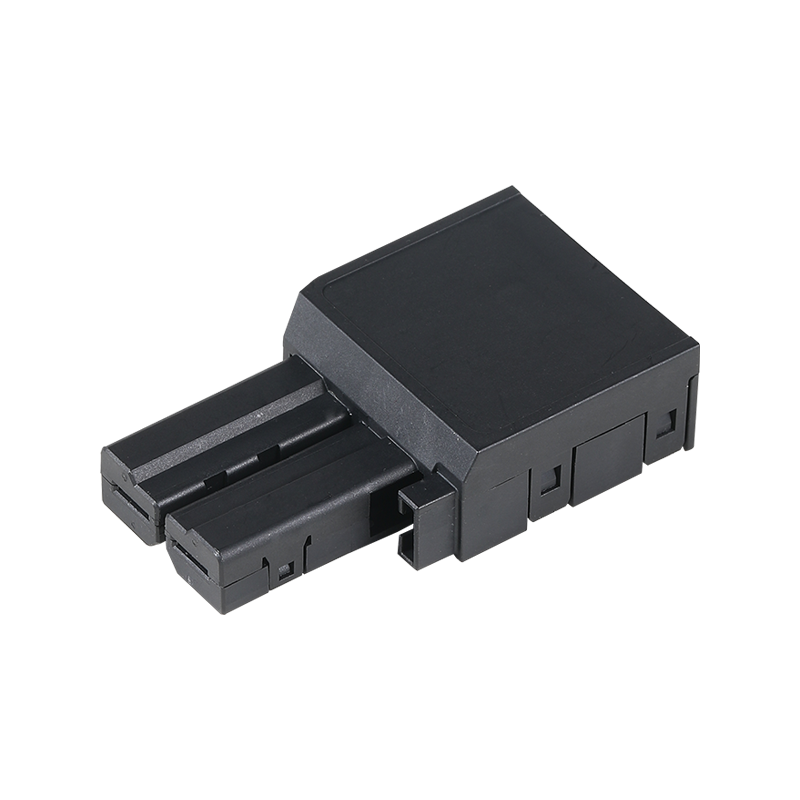
Precision mould parts, plastic foam molding, and automotive plastic mold are three critical areas that have seen significant advancements in recent years. These technologies are not only shaping the way products are made but also enhancing their performance and sustainability.
Precision mould parts are the backbone of many industries, particularly in the production of high-quality components that require exacting specifications. These parts are essential in ensuring that the final product meets the desired performance standards. The precision of these mould parts is crucial in industries such as aerospace, medical devices, and electronics, where tolerances are measured in microns.
The manufacturing process for precision mould parts involves the use of advanced machinery and materials. High-precision CNC machines are often employed to create the moulds, which are then used to produce parts with tight tolerances and smooth surfaces. Materials such as steel and aluminum are commonly used for their strength and durability, ensuring that the mould parts can withstand the pressures and temperatures of the moulding process.
Plastic foam molding is a process that involves the use of foam materials to create lightweight, yet strong, components. This technique is particularly useful in applications where weight reduction is a priority, such as in the automotive and packaging industries. The foam materials used in this process can be expanded polystyrene (EPS), polyurethane (PU), or polyethylene (PE), each offering different properties and benefits.
The process of plastic foam molding can be either through direct or indirect methods. In direct foam molding, the foam material is directly injected into the mould, while in indirect methods, a pre-expanded bead or pellet is used. The resulting parts are not only lightweight but also offer insulation properties, making them ideal for thermal and acoustic insulation applications.
The automotive industry has been at the forefront of adopting plastic moulding technologies to reduce vehicle weight, improve fuel efficiency, and enhance design flexibility. Automotive plastic moulds are used to produce a wide range of components, from interior trim to exterior body panels. The use of plastics in automotive applications has grown significantly due to their versatility and the ability to create complex shapes with intricate details.
Automotive Plastic Mold refers to the specialized molds used in the manufacturing process of plastic components for vehicles. These molds are designed to produce parts with high precision and durability, ensuring that the final products meet the stringent quality standards required in the automotive industry. They are utilized for creating a wide range of interior and exterior parts, from dashboards to bumpers, contributing to the vehicle's functionality and aesthetics.
Automotive plastic moulds are designed to withstand the rigors of the automotive environment, including exposure to various temperatures, chemicals, and physical impacts. The materials used for these moulds are carefully selected to ensure they can endure the high pressures and temperatures of the injection moulding process, as well as the long-term durability required for automotive components.
Precision mould parts, plastic foam molding, and automotive plastic mould are integral to the modern manufacturing landscape. They represent the intersection of technology, material science, and engineering, pushing the boundaries of what is possible in product design and production. As these technologies continue to evolve, they will undoubtedly play a significant role in shaping the future of manufacturing, offering solutions that are not only efficient but also sustainable and innovative.