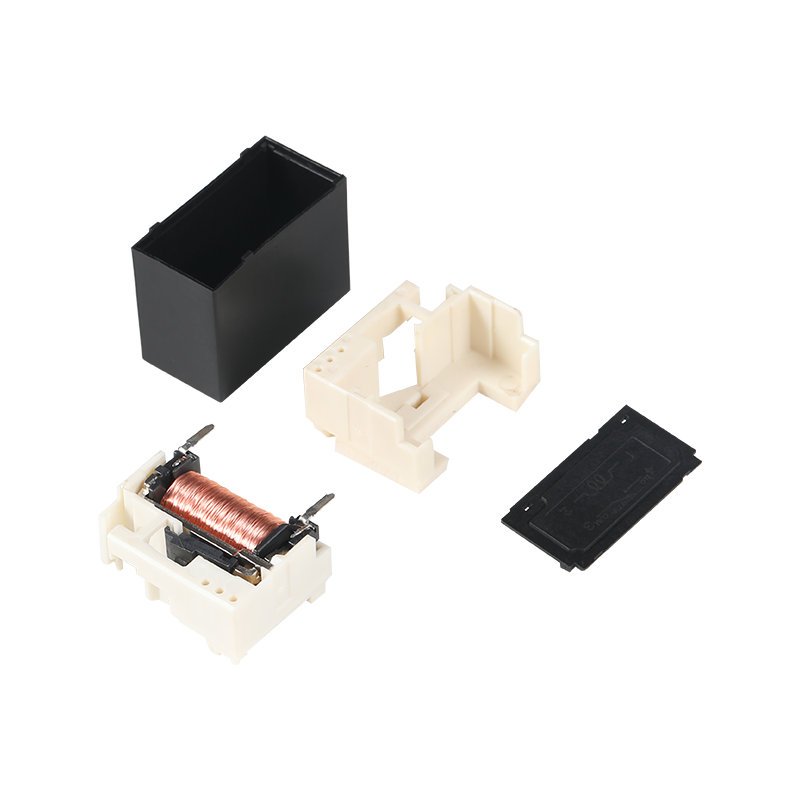
The automotive industry is a cornerstone of modern manufacturing, and a significant aspect of this industry is the production of car parts through various molding processes. Among these, injection molding stands out as a key technology for creating a wide range of components, from car bumpers to interior trims.
Car bumpers are critical components that serve both aesthetic and safety functions. They are designed to absorb impact during low-speed collisions, protecting the vehicle's body and passengers. The process of car bumper injection molding involves several steps:
Material Selection: High-impact-resistant plastics such as polypropylene (PP) and thermoplastic olefins (TPO) are commonly used due to their durability and flexibility.
Mold Design: The mold is designed to create the shape and features of the bumper, including any necessary reinforcements or attachment points.
Injection Moulding Process: Molten plastic is injected into the mould under high pressure, where it cools and hardens into the final shape.
Post-Moulding: Bumpers may undergo additional processes such as painting, coating, or assembly with other components.
The auto injection mould is a specialized type of injection mould used in the automotive industry. It is designed to withstand the high pressures and temperatures associated with automotive part production. Key features of auto injection moulds include:
Robust Construction: To endure the rigors of continuous production, these moulds are made from high-strength steel or aluminum alloys.
Precision Engineering: Tolerances in auto injection moulds are badly tight to ensure that each part produced is consistent and meets strict quality standards.
Quick Changeover: Many auto injection moulds are designed for quick changeovers to facilitate the production of different parts with small downtime.
Plastic is a versatile material used extensively in the automotive industry for a variety of parts, from exterior components to interior fittings. Molding plastic car parts involves several steps:
Material Preparation: Plastic pellets or granules are fed into the injection molding machine, where they are melted and prepared for molding.
Injection Moulding: The molten plastic is injected into the mould cavity, taking the shape of the part to be produced.
Cooling and Solidification: The plastic cools and hardens within the mould, maintaining its shape.
Ejection: Once the part is fully formed, it is ejected from the mould and can be inspected, finished, or assembled.
Advantages of Molding in the Automotive Industry
Injection molding is a cost-effective method for mass-producing complex parts with intricate details.
The process allows for a wide range of designs, from simple shapes to complex, multi-component structures.
Injection molding uses materials efficiently, with small waste, which is beneficial for both cost and environmental considerations.
The parts produced through injection molding are known for their durability and strength, which is crucial for automotive applications.
Injection molding is a cornerstone technology in the automotive industry, enabling the production of high-quality, durable, and complex car parts. From car bumpers to intricate interior components, the process plays a vital role in shaping the vehicles we drive today. As technology advances, we can expect further innovations in molding techniques, materials, and automation, continuing to push the boundaries of what is possible in automotive design and manufacturing.