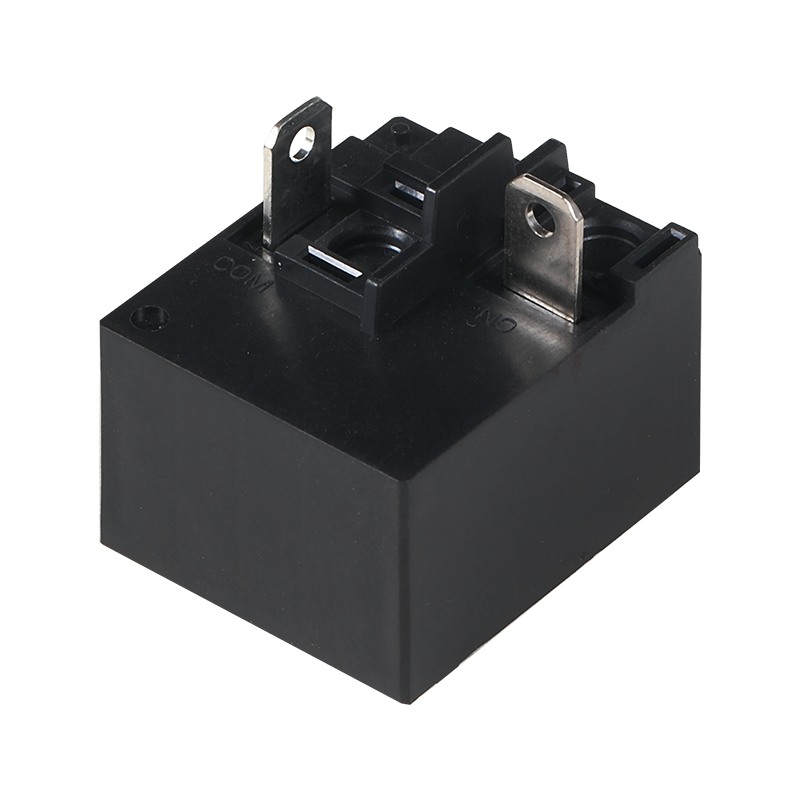
Injection molding is a manufacturing process that has become an integral part of the production of various plastic parts and components. It is a high-volume, efficient method used across industries such as automotive, consumer goods, electronics, and medical devices.
The process of injection molding involves the use of a machine that heats and melts plastic material, which is then injected into a mold cavity. The mold is designed to create the desired shape and features of the final product. Once the plastic cools and hardens, the mold opens, and the finished part is ejected. Large scale injection molding refers to the production of a large number of identical parts in a short period, which is made possible by the automation and efficiency of the process.
The setup cost for injection molding can be high, but the cost per unit decreases significantly with large production runs, making it an economical choice for mass production.
Injection molding machines can produce parts with high dimensional accuracy and consistency, which is crucial for parts that need to fit together or meet strict specifications.
A wide range of thermoplastic materials can be used in injection molding, allowing for the production of parts with different properties such as strength, flexibility, and heat resistance.
Parts with complex geometries, including undercuts and intricate details, can be produced with relative ease, which is not always possible with other manufacturing methods.
The process can be highly automated, reducing labor costs and increasing production speed.
The cost of injection molding machines and molds can be substantial, which may be a barrier for small businesses or startups.
Molds require regular maintenance and can be expensive to repair or replace, especially for large-scale production runs.
While the process is efficient, there can still be waste from sprues and runners, which are parts of the injection molding process that do not become part of the final product.
The process requires significant energy to heat and cool the materials, which can be a concern for environmentally conscious manufacturers.
While injection molding can produce complex parts, there are still design limitations that must be considered, such as the need for draft angles and the inability to produce parts with overhanging features without support.
There is a growing focus on reducing waste and energy consumption in injection molding. This includes the use of recycled materials, energy-efficient machines, and processes to small material waste.
The development of new materials, such as biodegradable plastics, is expanding the possibilities for injection molding in industries that prioritize sustainability.
The integration of robotics and advanced automation is expected to further increase the efficiency and precision of the injection molding process.
The use of digital technologies, such as 3D printing for mold making and simulation software for process optimization, is becoming more prevalent.
While large scale injection molding is traditionally associated with mass production, there is a growing trend towards mass customization, where small variations are made to meet individual customer needs.
In conclusion, large scale injection molding is a powerful manufacturing technique that offers significant benefits for high-volume production. Despite the challenges, the future of large scale injection molding looks promising, with innovations set to shape the way we produce plastic parts for years to come.