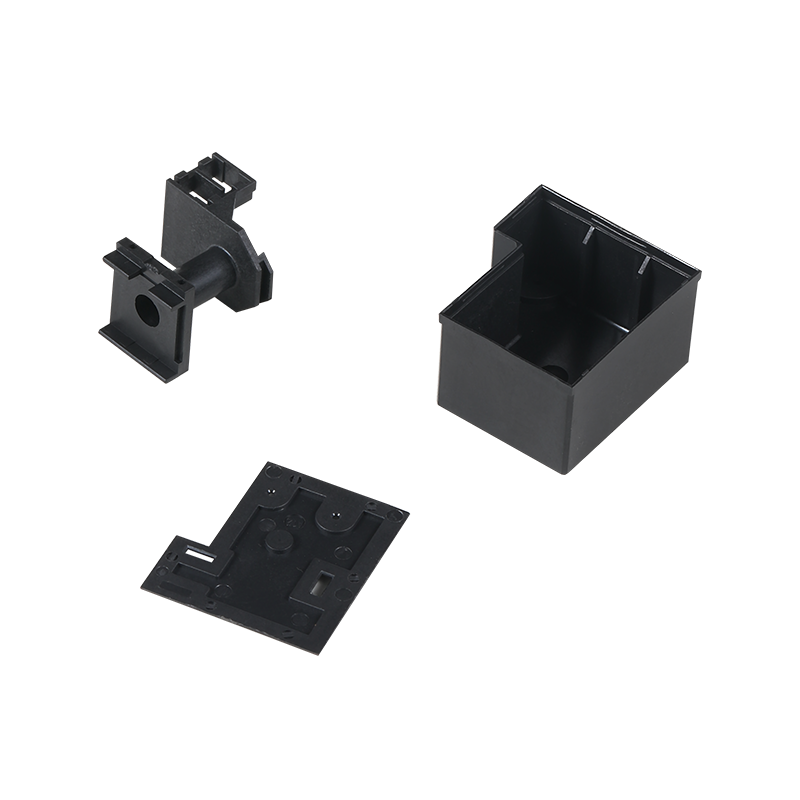
Injection molding is a widely used manufacturing process in the production of plastic parts and components. This process involves injecting molten material into a mold to create items with precise dimensions and complex shapes. Among its various applications and advancements, multi-shot injection molding, bumper injection molding, and sustainable injection molding have gained prominence for their unique attributes and contributions to different industries.
Multi-shot injection molding, also known as two-shot or multi-component molding, is a process where two or more different materials or colors are injected into a mold to create a single, integrated part. This method offers several benefits, including enhanced product functionality, improved aesthetics, and cost-efficiency.
The process involves sequential or simultaneous injection of materials into a mold. It is commonly used for products that require a combination of rigid and flexible sections or varied colors. For instance, handles with a soft grip often use this technique, combining a rigid plastic frame with an over-molded rubber-like material for added comfort and durability.
Industries such as consumer goods, medical devices, and automobiles benefit from multi-shot injection molding, as it allows for integrating multiple features without additional assembly steps.
Bumper injection molding specifically addresses the needs of the automotive sector, where durability, safety, and design are critical. Bumpers, which serve as protective barriers in vehicles, must meet strict performance and aesthetic standards.
This process typically involves the use of thermoplastic materials, which are lightweight yet strong enough to absorb impact. Materials like polypropylene and other polymer blends are frequently used for this purpose. The molding process ensures that the bumpers are not only robust but also dimensionally accurate, allowing for seamless integration with vehicle structures.
Design flexibility is another significant advantage of bumper injection molding. It enables the production of complex shapes and features, such as slots for fog lamps or air intakes, while maintaining a high level of precision. The automotive industry values this process for its ability to produce large parts efficiently and with consistent quality.
Sustainable injection molding focuses on small environmental impact by optimizing materials, processes, and energy consumption. With growing awareness of environmental concerns, manufacturers are increasingly adopting eco-friendly practices in injection molding.
Key strategies in sustainable injection molding include:
Use of Recycled Materials: Recycled plastics are being incorporated into production processes to reduce reliance on virgin materials and decrease waste.
Energy-Efficient Machinery: Modern injection molding machines are designed to consume less energy, reducing carbon emissions during production.
Design for Recycling: Parts are designed to be easily recyclable, ensuring that they can be reprocessed at the end of their life cycle.
Material Reduction: Efforts are made to optimize part designs to use less material while maintaining functionality.
Sustainable injection molding is finding applications across industries, from packaging to automotive, aligning with global goals for reducing environmental impact and promoting circular economies.
The evolution of injection molding processes such as multi-shot injection molding, bumper injection molding, and sustainable injection molding highlights the industry's adaptability to diverse needs and challenges. Whether it is creating multi-functional parts, ensuring vehicle safety, or reducing environmental footprints, these processes demonstrate the versatility and potential of injection molding in modern manufacturing.