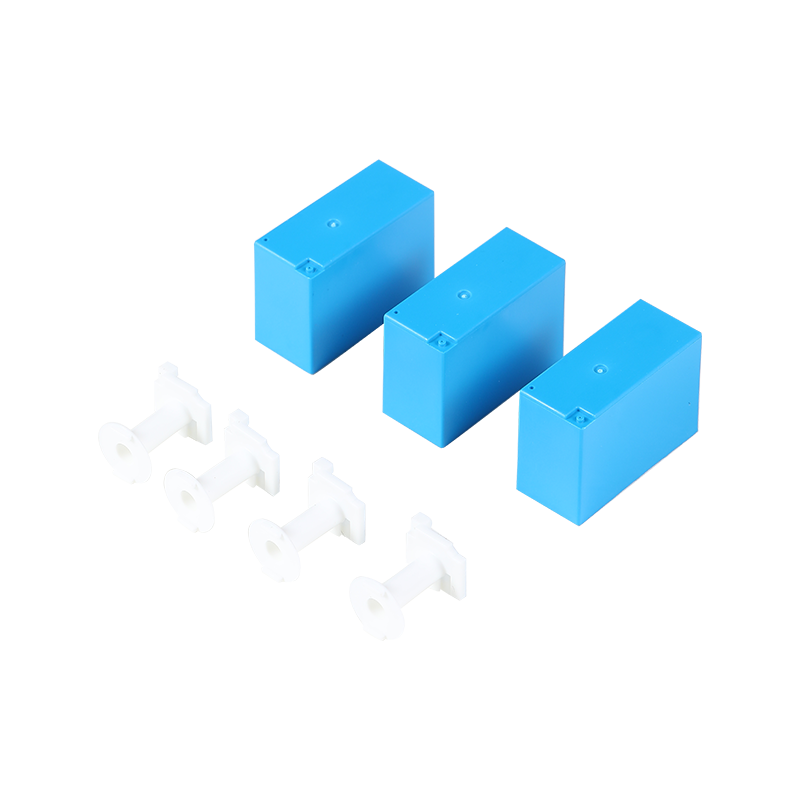
The automotive industry has long been at the forefront of innovation, constantly seeking ways to improve efficiency, performance, and safety. One such innovation is the use of plastic injection molding for the production of automotive parts. This process has revolutionized the way cars are manufactured, offering a range of benefits from cost-effectiveness to weight reduction.
Plastic injection molding is a manufacturing technique that involves the use of a mold to shape plastic material. The process begins with the plastic material, typically in the form of pellets, being fed into a hopper. It is then heated and melted in a barrel, where it is mixed and forced into a mold cavity. Once the mold is filled, the material cools and hardens, taking the shape of the cavity. The mold is then opened, and the finished part is ejected. This process is highly automated and can produce parts in large quantities with a high degree of precision.
Car part molds are designed to produce a wide range of components, from small interior fittings to complex exterior parts. Some of the more common automotive parts produced through plastic injection molding include:
1. Dashboards: These are large, complex parts that require precise molding to ensure a good fit and finish.
2. Bumpers: Molded to absorb impact and protect the vehicle during collisions, they are often made from a combination of materials for strength and flexibility.
3. Light Housings: These protect the vehicle's lighting systems and are designed to withstand high temperatures and weather conditions.
4. Interior Trim: Components such as door panels, center consoles, and instrument panels are often made from molded plastic for a consistent and aesthetically pleasing finish.
5. Exterior Components: Parts like grilles, spoilers, and body panels can be molded to achieve a smooth, seamless appearance.
The use of plastic injection molding in the automotive industry offers several advantages:
1. Cost-Effectiveness: The process is highly efficient, allowing for the production of large quantities of parts at a lower cost compared to traditional manufacturing methods.
2. Lightweight: Plastic parts are lighter than their metal counterparts, which can contribute to improved fuel efficiency and reduced emissions.
3. Design Flexibility: Injection molding allows for the creation of complex shapes and designs that may not be possible with other materials.
4. Durability: ABS and other plastics used in automotive parts are resistant to corrosion and can withstand harsh weather conditions.
5. Recyclability: Many plastics used in automotive parts can be recycled, contributing to a more sustainable manufacturing process.
While plastic injection molding offers numerous benefits, there are also challenges to consider. The initial cost of mold creation can be high, and the process requires careful material selection to ensure parts meet the necessary strength and durability standards. Additionally, the environmental impact of plastic production and disposal must be managed responsibly.
Plastic injection molding has become an integral part of the automotive industry, offering a cost-effective and efficient method for producing a wide range of car parts. As technology continues to advance, the capabilities of plastic injection molding are likely to expand, further enhancing its role in the manufacturing of automotive components. With a focus on innovation and sustainability, the future of plastic injection molding in the automotive sector looks promising.