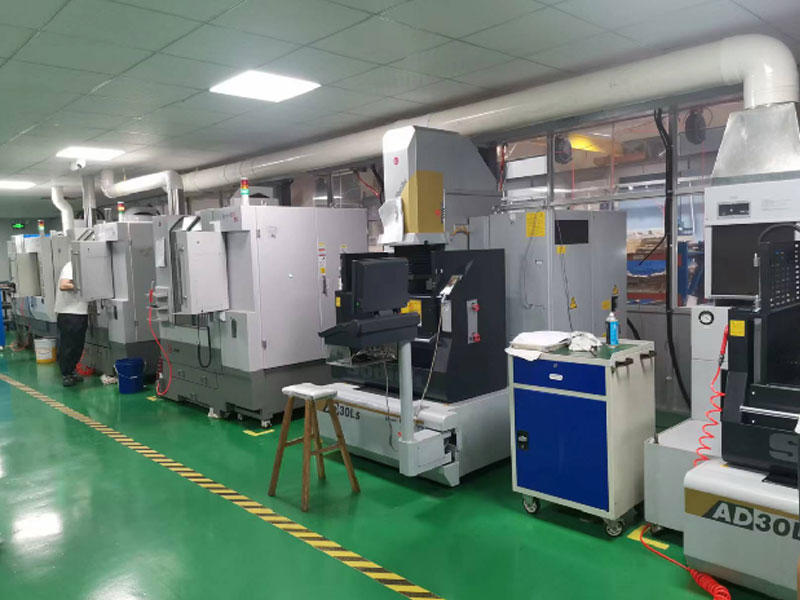
abs molding Wholesaler Exporter
ABS (Acrylonitrile Butadiene Styrene) molding is a versatile and widely used manufacturing process that allows for the creation of complex and durable plastic parts. This thermoplastic polymer is favored in various industries due to its outstanding mechanical properties, including impact resistance, chemical resistance, and ease of processing. The ABS molding process encompasses several techniques, including injection molding, extrusion, and thermoforming, each with its unique advantages and applications.
Injection molding is perhaps the common method of ABS molding. In this process, ABS pellets are heated until they melt and then injected into a mold cavity under high pressure. This technique is ideal for producing high volumes of parts with intricate designs, such as automotive components, consumer electronics, and household appliances. The precision of injection molding allows manufacturers to achieve tight tolerances and complex geometries, making it a popular choice for many applications. The ABS molding process in injection molding is efficient, as it minimizes waste and can produce parts quickly, making it cost-effective for large production runs.
Extrusion is another significant method of ABS molding. In this process, ABS is heated and forced through a die to create continuous shapes, such as sheets, tubes, or profiles. The extruded ABS can then be cut to length or further processed into finished products. This technique is particularly useful for applications requiring long, uniform shapes, such as pipes, panels, and various construction materials. The flexibility of extrusion allows for the incorporation of additives and fillers, enhancing the properties of the product. The ABS molding process in extrusion is characterized by its ability to produce large quantities of material with consistent quality.
Thermoforming is a third method of ABS molding that involves heating a sheet of ABS until it becomes pliable and then forming it over a mold. This technique is commonly used for creating larger parts, such as automotive interiors, packaging, and appliance housings. The thermoforming process can be divided into vacuum forming and pressure forming, each offering different levels of detail and complexity in the final product. Vacuum forming is simpler and more cost-effective, while pressure forming allows for more intricate designs. The ABS molding process in thermoforming is advantageous for low to medium production volumes, as it requires less investment in tooling compared to injection molding.
Each of these ABS molding techniques has its specific considerations and requirements. For instance, in injection molding, controlling the temperature and pressure is crucial to avoid defects such as warping or incomplete filling. In extrusion, maintaining a consistent temperature and flow rate ensures uniformity in the extruded product. Thermoforming requires careful temperature control to achieve the right pliability of the ABS sheet, ensuring it conforms well to the mold without tearing or creating weak spots.
The choice of ABS molding method often depends on the desired characteristics of the product, production volume, and cost considerations. For high-volume production with complex geometries, injection molding is typically the better option. For simpler, longer parts, extrusion may be more suitable. Thermoforming is ideal for larger parts where detail is less critical, and lower production volumes are acceptable.
ABS molding is a critical process in modern manufacturing, offering a range of techniques that cater to various applications and industries. The versatility of ABS, combined with the efficiency of these molding methods, makes it a popular choice for producing durable and high-quality plastic parts. As technology advances, the ABS molding processes continue to evolve, allowing for even greater innovation and efficiency in the production of plastic components. Whether through injection, extrusion, or thermoforming, ABS molding remains a cornerstone of the plastics industry, driving the creation of products that enhance our daily lives.