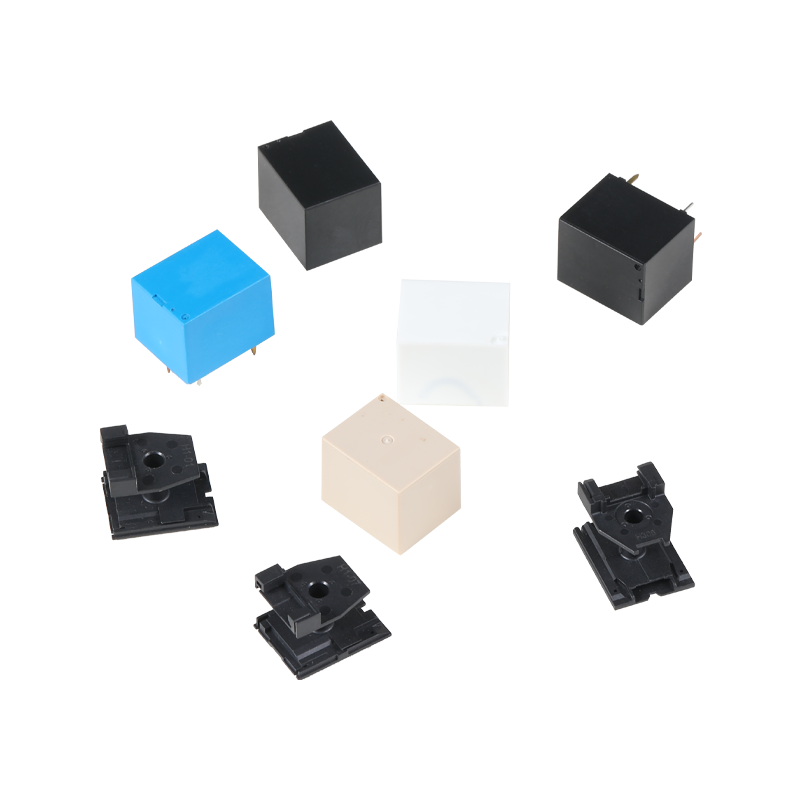
Dual shot injection molding and twin shot injection moulding are advanced techniques that have revolutionized the way complex and multi-material parts are created. These processes offer a multitude of benefits, from enhanced aesthetics to improved functionality.
Small molded parts are ubiquitous in our daily lives, found in everything from electronic devices to automotive components. These parts are typically produced using injection molding, a process where molten material is injected into a mold cavity and allowed to cool and solidify. The precision of this method allows for the creation of intricate details and high-quality finishes. Small molded parts are often used in applications where size, weight, and material properties are critical, such as in the aerospace, medical, and consumer electronics industries.
Dual shot injection molding, also known as two-shot molding, is a process that involves injecting two different materials into a single mold to create a part with two distinct layers. This technique allows for the combination of materials with different properties, such as soft and hard plastics, to create parts that are both functional and aesthetically pleasing. The dual material approach can enhance the part's durability, comfort, and appearance. For instance, a handle might have a soft grip made of one material and a structural body made of another, providing both comfort and strength.
Twin shot injection moulding is a variation of the dual shot process, where two different materials are injected simultaneously into the mold from separate nozzles. This method allows for even more precise control over the placement and thickness of each material layer. The result is a part with a seamless integration of materials, which can be particularly useful in applications where the transition between materials must be smooth and consistent. Twin shot molding is often used in the production of high-end consumer goods, where the combination of materials can create a unique look and feel.
The applications of small molded parts, dual shot injection molding, and twin shot injection moulding are vast and varied. In the automotive industry, these techniques are used to produce lightweight components that can improve fuel efficiency while maintaining strength. In the medical field, they enable the creation of multi-material devices that can be both sterile and comfortable for patients. Consumer electronics benefit from the ability to combine conductive and insulating materials in a single part, reducing the need for multiple components and assembly steps.
The benefits of these processes extend beyond the functional. Aesthetics play a significant role in product design, and dual shot and twin shot molding allow for the creation of parts with unique textures and colors. This can pilot products that are not only practical but also visually appealing, which can be a key differentiator in competitive markets.
While the benefits of small molded parts, dual shot injection molding, and twin shot injection moulding are clear, there are challenges to consider. The complexity of these processes can pilot higher initial costs, both in terms of equipment and material. Additionally, the design and engineering of molds for these processes require specialized knowledge and expertise.
Small molded parts, dual shot injection molding, and twin shot injection moulding are integral to the modern manufacturing landscape. They offer a range of solutions for creating parts that are both functional and visually appealing. The future of manufacturing is poised to be shaped by these versatile and efficient techniques, ensuring that the products we rely on are not only high-performing but also designed with precision and care.